TUTORIAL LESSON 17 |
Welcome to the Prince August Tutorial on making a Fantasy Armies Catapult set. This month we concentrate on casting and assembling our 25mm Catapult (No.673) and crew (No.672) from our Fantasy Armies series.
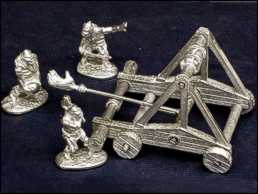
These are a great set, and add some pretty destructive elements to any battle. Hurl balls of fire, or shards of rock, or even dead enemies at your opponents with this catapult. Remember as these are molds you can cast a huge amount of these catapults and bombard your foes forthress into submission.
You will need our Casting starter kit PA2000, some Model Metal and a metal file and clippers.
|
Casting the catapult. |
The Difference between this catapult mold and many others is that you need to cast it multiple times to get all the parts you need. You can remelt all the surplus afterwards.
- Make sure your mold is dry and free of dirt, then gently heat the mold to reduce stiffness. It should be warm when you start casting. There are two molds in the catapult set.
- Make sure you dry the release powder as well, there should be no clumps in it. Then use some clean cotton wool to spread it evenly over the entire mold, on both sides, and make sure you get it into all the dips as well, not just the raised parts.
- Once you have completed that, take both sides and clap them together 4 or 5 times to remove excess powder. Do NOT rub them together, just a nice crisp 'clap'. It should remove all loose powder.
- Close the mold halves together and add the support boards (rough side against the mold so it does not slide about). The Support boards protect the molds from the clamps marking them and also spreads the pressure better across the entire surface of the mold.
- If you wish you can add a second set of clamps to both sides. I find this works very well. Clamp them about an inch into the mold, so the sides are held shut, otherwise metal may leak. If you clamp to close to the edge the clamps may fall off when pouring the metal so use your judgment. ALWAYS clamp both sides of the mold. You can use elastic bands as additional support if you wish. DO NOT clamp too tightly or you may constrict the flow of the metal.
- Heat the metal in the ladle as normal, we used Model Metal, as it is the easiest to cast. If you use gas flame instead of a hotplate then put a flat saucepan over the flame first to create a substitute 'hotplate' and use the ladle then. This creates a more even heat. Test the metal is at the right temperature with a used match, dip the wooden end into the metal and if it smokes lightly it is ready. If it smokes heavily, you have it too hot. Scrape away any scum deposits off the top and then pour steadily into the mold hole, avoid splashing and fill the mold to the brim with the metal. This is important. The weight of the metal forces the metal into all the areas of the mold. So if you do not have enough metal to fill the mold you will not get a proper cast. As you pour the metal, tap the top of the mold gently with something solid to help settle the metal.
- When finished pouring the metal, continue tapping the mold gently but firmly until the metal begins to set. Do not tap after that or you may cause cracks to form in the cast. Tapping the still hot metal helps fill the mold.
- Give about 5 minutes to cool, or use that time to cast the other mold, then open this mold gently. You can see if any gaps are present, or excessive flashing (bleeding of metal) has occurred. If you are not satisfied then remelt the metal and try again. If you are happy with the cast then bend the mold away from the casting, Do NOT pull the casting out of the mold as that can result in tearing of the soft mold.
- Cast both molds. You will need to cast one mold 4 times to get the 4 wheels of the catapult and the 2 sides. You only need to cast the other mold (with the catapult throwing arm) twice to get both axles and winding mechanisms.
- You should have 4 casting of the sides of the catapult and 2 casting of the throwing arm part of the catapult. Now use a clippers to carefully cut away the excess sprues and separate the parts. Generally use the flat side of the clippers against the area you want to keep and the curved part against the sprue (waste part). If you find certain parts difficult to reach, cut away parts around it to make it easier to reach. It is wiser to leave a little excess metal on a part than cut too close as you can always file that part afterwards to clean it up.
- Once all the parts are cut away you can clean them up. Use a sharp knife to cut away any 'Flash' metal. Flash metal is where the metal has bled out between the mold seems. It is easily removed. All metal removed can be reused.
- Use the file to clean the parts and remove any unwanted seems that might show up. Clean the axles and connecting parts so they will fit snugly together.
- You may have to clean the holes in the casting if the parts do not fit easily. This helps with glueing too. Just twist a knife around to remove any tiny lumps or ridges that exist.
- Finally you should have all the parts ready for assembly. You should have 2 sides of the wooden part of the catapult, the throwing arm, 2 axles, 4 wheels, the padded top bar that stops the arm when fired, the winding bar (where the rope should be) and 2 ends for that bar that have holes for the orc to use a stick to wind it.
|
|
|